LCC/QFN Type Devices
These type of devices are soldered directly to the PCB with the expectation to achieve a low profile connection.
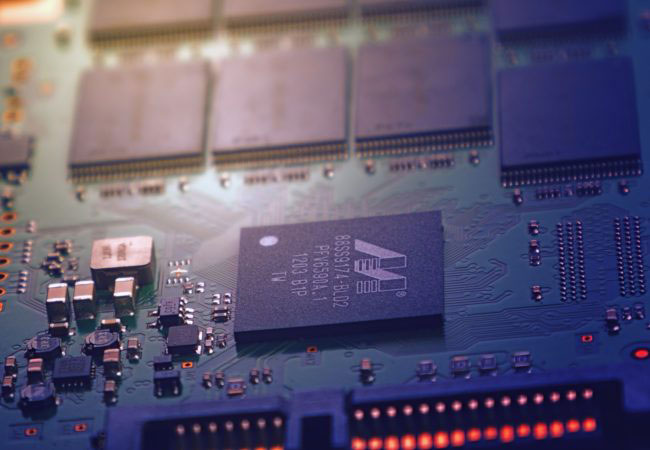
However, this can create problems.
The solder connection between IC and PCB is very thin, and susceptible to fracture when subject to vibration CTE (Coefficient of Thermal Expansion) issues can occur when the IC gets warm during operation and the PCB does not. The two expand at different rates and this can crack the solder joints.
Potential Failure Points
Typical solder joint cracking occurs due to fatigue failure during thermal cycling. Major difference in CTE (Co-efficient of Thermal Expansion) and vibration between ceramic LCC body and PEC substrate. Solder is a fairly weak alloy that can not withstand cyclic stresses easily. Cycles to failure will be low and reliability in service poor as a result.
Cross-section of fatigue failure showing crack travelling through bulk of solder. Note very low solder thickness under the component.