safety & precision in medical electronics
The importance of electronic device reliability in healthcare and how Retronix can help.
Similar to Defense and Aerospace, the Health care industry has high standards to support the safe manufacture and operation of medical-grade devices. Reliability, precision, and safety are the top considerations for designing electronics for medical devices. With the main objective to protect the health and safety of patients.
Hand in hand, with the advancement of medical science and treatments, electronics too have become more sophisticated and efficient. With rapid improvements in technology and the miniaturization of electronic devices, electronic equipment has also shrunk in size and increased in component density.
Such electronic equipment used in health care settings includes biological sensors, ventilators, and defibrillators, all of which perform life-critical functions. Therefore, it’s imperative that medical devices cannot fail under any circumstances as errors can prove fatal. Additionally, healthcare professionals rely on electronic equipment to provide critical data and stats, and therefore, precision is vital.
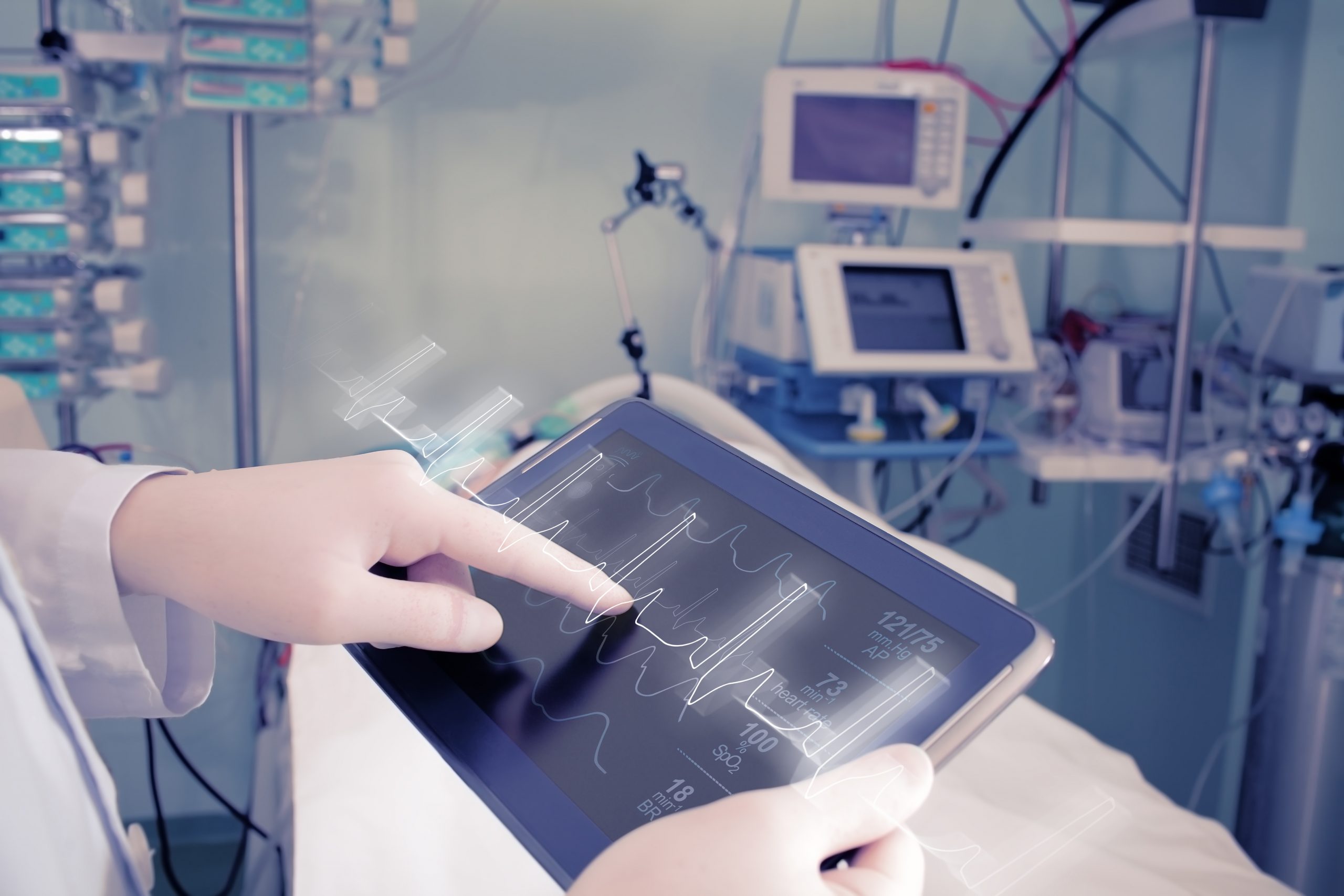
Factors that Effect Reliability in Medical Electronics
Despite the gravity of precision and reliability in medical electronics, even the most efficient devices can fail. Such failures can be caused by a myriad of manufacturing faults or failures in electronic components including fuses, relays and oxidation.
The electronic devices and components used in medical electronics are subject to and encounter the same problems as other reliability industries in the defense, and aerospace sectors:
- Obsolescence Issues
- Solderability Issues
- RoHS Compliance Issues
- Shortage and Allocation
- Procurement of Critical Devices
Our Solutions for Medical Electronics
ALLOY CONVERSION: As medical devices are no longer RoHS exempt, manufacturers now need to source lead-free electronic components to ensure that their equipment is compliant. Retronix can convert your leaded (Pb) components to lead-free using our fully automated Alloy Conversion system. Our technology ensures that devices aren’t exposed to excess heat or abrasion, meeting the stringent High-Reliability GEIA Standard. We are one of the few companies in the world to offer a full bill of material (BOM) process. We can then confirm alloy using our in-house XRF system. We offer lead-free to tin/lead conversion, and vice versa. Learn More.
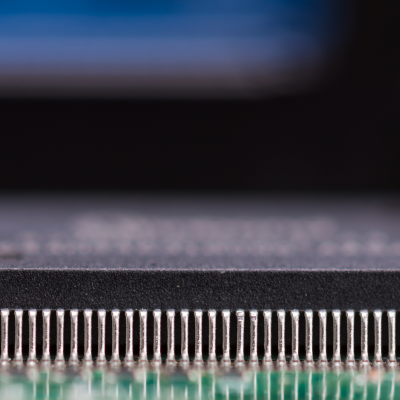
Alloy Conversion
COUNTERFEIT TESTS: Globally around 8-10% of all medical devices are of fake origin, this number will no doubt increase as a result of the global chip shortage. Retronix has not only seen significant growth of customer requirements for our testing services. Alarmingly, the quantity of counterfeit chips and suspicious components that we are detecting has risen significantly also. Retronix has a test department dedicated to the identification of counterfeit parts along with the best tools for this process. We also have years of experience earned from dealing with this issue for numerous customers in varying industry sectors. Learn More.
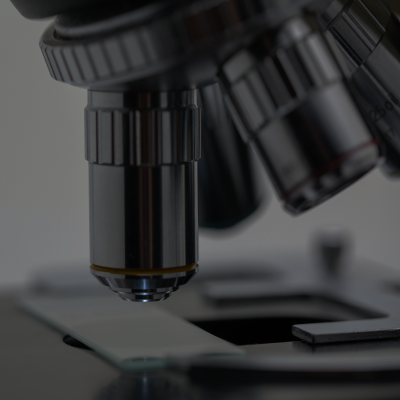
Counterfeit Tests
HIGH PRECISION REWORK: Rather than discarding medical equipment that may have fused or tripped PCB Repair offers a much more cost-effective option. Retronix can carry out a circuit board repair on any PCB with physical damage. Our suite of repair and rework services are carried out in our fully ESD compliant facility. We operate to recognised IPC and JEDEC standards and our skilled workforce is trained and continually assessed by our on-site trainers.
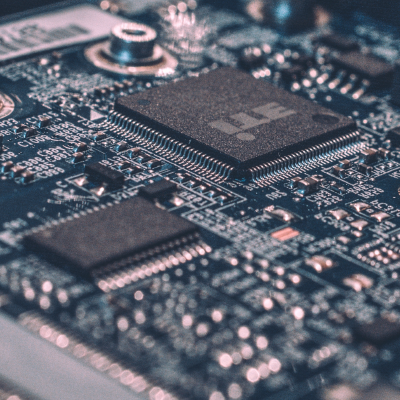
PCB Rework
HIGH-VALUE COMPONENT RECLAIM: High Reliability components are used on multiple systems and can often be found on unused, but obsolete PCBs within system manufacturers. These components are known and have had zero hours of use, so recovering them is a better option than buying supposedly “brand new” components from the gray market. Retronix has developed a component reclaim process which avoids reflow cycles. Operating to IPC-9592 STD, our leading technology, including Laser Reballing, delivers the safest recovery and refurbishment service in the industry. Learn More.
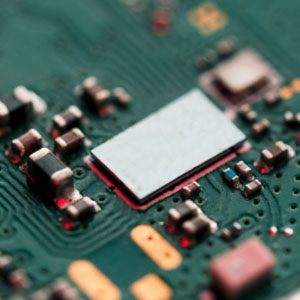
Component Reclaim
Customer Feedback
” I’d like to take this opportunity to thank everyone who has supported the quick turnaround of products that are critical to our end customer in the fight against COVID-19. The quality of the work was exceptional, the quick turnaround times made a huge difference and service from start to finish provided by Retronix far exceeded our expectations, all of this has resulted in critical products being sent to our customers on time and now available for use in the fight against COVID-19. Whilst we steer our way through the course of this virus all at Retronix should be proud of the part they played in trying to control and defeat this virus”.
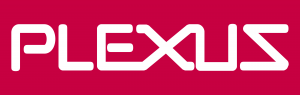
“Retronix are committed to supporting our customers who are manufacturing ventilators or critical medical equipment in the fight against COVID-19. Retronix Re-tinned 1200 devices in less than 5 days enabling Siemens Healthcare – Medical Electronics divsion to restart their production line and increase their supply of ventilators to the market”.