Alloy Conversion
The High-Reliability sector is exempt from RoHS compliance due to issues associated with lead-free solder. Reintroducing lead into the alloy finish on an IC is seen as the best way to avoid issues such as tin whiskers.
Retronix offers a fully automated solder dip process, that complies with the High-reliability industry standard ANSI/GEIA Standards.
Our process offers repeated dip length, dwell time and temperatures on the smallest of chip components up to the largest QFPs’ and thru-hole components.
We can then confirm alloy using our in-house XRF system. We offer lead-free to tin/lead conversion, and vice versa.
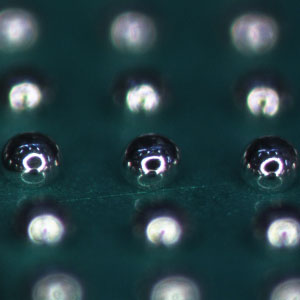