convert alloy on devices
Retronix offers a fully automated solder dip process, that complies with the high-reliability industry standard ANSI/GEIA standards.
Our process offers repeated dip length, dwell time and temperatures on the smallest of chip components up to the largest QFPs’, and thru-hole components.
We can then confirm alloy using our in-house XRF system. We offer tin/lead to lead-free conversion, and vice versa.
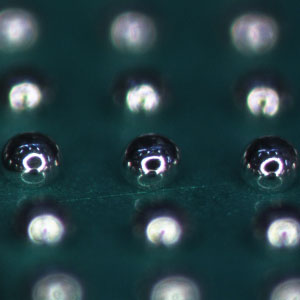