Obsolescence Management: Extend the Life of Electronics
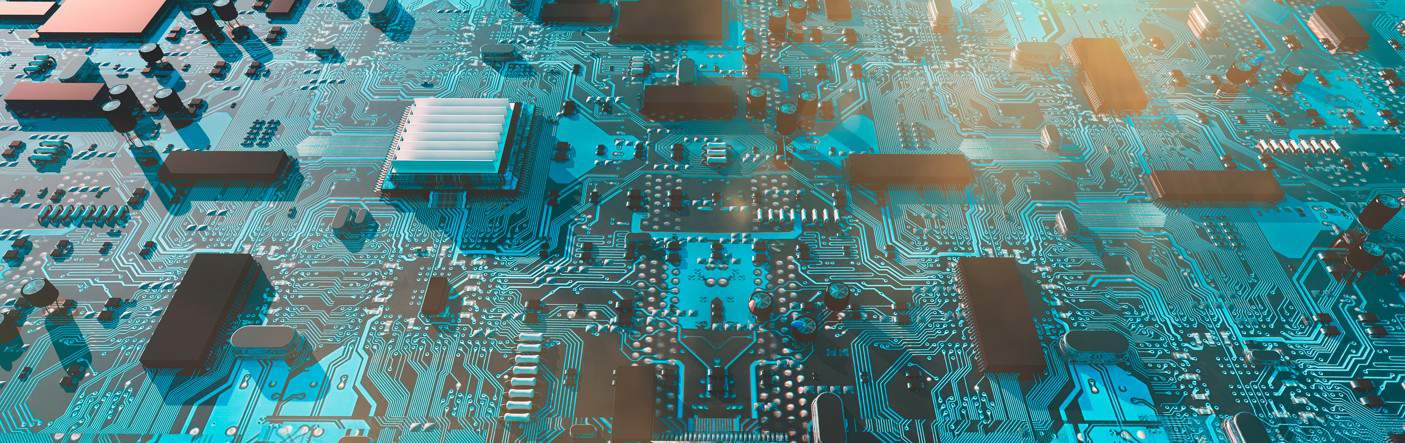
In industries like aerospace, defence, automotive, railway, and medical; products are built to last.
Aircraft, military systems, trains, and medical devices often remain in service for decades. However, their electronic components have a much shorter lifecycle. Component manufacturers may stop production within just a few years, leaving companies to face the daunting challenge of component obsolescence.
The Challenge of Obsolescence
Once a component becomes obsolete, it is no longer available through authorised channels. This can halt production lines, disrupt maintenance schedules, and lead to costly redesigns. With suppliers no longer offering support, companies must find alternative ways to source or manage these critical parts.
Counterfeit components are another growing threat. Desperate to keep operations running, some businesses turn to unreliable sources, which bring significant risks.
Aerospace and Defence: These sectors often face extended operational lifespans for their products, with aircraft and defence systems in service for decades. Component obsolescence can lead to expensive redesigns, extended maintenance times, or the need to reverse-engineer obsolete parts.
Automotive: Vehicle manufacturers often deal with rapid technological advancements. However, maintaining electronic components for older car models remains crucial, particularly for specialised or commercial vehicles. The lack of original parts can create significant supply chain bottlenecks.
Railway: Trains are designed to operate for 30 years or more, leading to challenges in sourcing outdated electronic parts. Component failures can cause significant operational disruptions, while redesigning and validating replacements can be both time-consuming and costly.
Medical Devices: Strict regulatory standards mean that replacing components in medical devices requires extensive testing and validation. Obsolescence can lead to significant compliance challenges, making proactive planning essential to avoid device downtime.
These sectors often establish strategic reserves of components and leverage long-term supplier agreements
What is Obsolescence Management?
Obsolescence management refers to the proactive strategy of anticipating, mitigating, and managing the risks associated with components becoming obsolete. It is an essential aspect of maintaining operational efficiency and reducing the costs associated with the downtime caused by discontinued parts. Companies that manage obsolescence effectively can avoid supply chain disruptions and extend the life of their products.
Retronix Solutions
Retronix provides several essential services designed to address obsolescence challenges. These services offer businesses the opportunity to recover, refurbish, and reuse components, thereby minimizing waste, saving costs, and ensuring sustainability in their supply chains. Some of the key services include:
Recovery and Reuse of ICs: With companies upgrading equipment frequently, valuable ICs can often be salvaged and reintroduced into the supply chain. Retronix specializes in recovering these ICs, ensuring they are functional and meet industry standards, preventing them from ending up in landfills. By reusing high-quality components, companies can avoid sourcing expensive, obsolete parts from secondary markets.
Reballing: Reballing involves replacing the solder balls on a ball grid array (BGA) package to ensure proper functionality and alignment on printed circuit boards (PCBs). This process is vital when recycling or refurbishing IC’s because the IC’s can be seamlessly integrated into new systems, especially if the original solder has degraded or the alloy needs to be updated to meet new standards.
Retinning: When IC leads have been exposed to oxidation or contamination over time, retinning can restore them to optimal condition. By applying fresh solder to the leads, Retronix ensures proper conductivity and adhesion, extending the usability of components. This is particularly important for IC’s that have been in storage or are being repurposed for new applications.
Alloy Conversion: In some cases, ICs may require an update to the solder alloy used, especially if they were originally manufactured with lead-based solder. Alloy conversion involves replacing the existing solder with compliant materials, making components suitable for contemporary manufacturing processes, and ensuring long-term reliability.
IC Testing: Ensuring that refurbished or recovered IC’s are fully functional and meet performance standards is critical in obsolescence management. Retronix offers comprehensive IC testing services, including functional and parametric testing, to verify the integrity of components. This testing process helps companies avoid costly system failures by ensuring only reliable components are put back into circulation.
As industries continue to face the challenges of obsolescence, the need for efficient management strategies becomes more critical. Retronix’s suite of services—including recovery and reuse, reballing, retinning, alloy refresh, and IC testing provides businesses with the tools to mitigate the risks of obsolescence, extend the life cycle of their electronic components, and ensure long-term sustainability. By partnering with Retronix, companies can not only reduce costs and improve reliability but also contribute to a greener, more sustainable future in electronics manufacturing.
If you found this article informative, you may also find this one (click here) to be of interest. It delves into related topics, providing further insights and perspectives that complement the content discussed here.