Is Your Supply Chain Safe? Combat the Threat of Counterfeit Electronic Components
The electronics industry is a vast and intricate network that drives everything from consumer gadgets to aerospace systems. However, a persistent threat lurks within this supply chain: counterfeit electronic components. These fake parts can lead to devastating consequences, including system failures, financial losses, and safety hazards. Implementing robust safeguards is crucial for manufacturers, suppliers, and governments alike.
Counterfeit electronic components are a growing concern. A study conducted by U.S. Department of Commerce, found that the semiconductor industry is anticipating challenges because of geopolitical tensions and potential supply disruptions. Counterfeiters are taking advantage of these issues.
The report assesses counterfeit electronics within the defense industrial base. It highlights that counterfeit incidents increased, and primarily involved integrated circuits and semiconductors. Companies report challenges in detecting counterfeits, with 39% of cases causing financial loss. Over 50% of companies experienced counterfeits in the last two years (when the study was conducted). Improved testing, stricter supplier vetting, and enhanced legal actions are recommended to mitigate risks. These findings were reported in 2010, with the situation now understood to be significantly worse.
Why are counterfeits dangerous?
System Failures: Fake components can malfunction, leading to catastrophic failures in critical systems such as medical devices, defence equipment, or automotive safety systems.
Financial Losses: Companies may face expensive recalls, legal liabilities, and reputational damage.
National Security Risks: Counterfeit parts in military applications could compromise sensitive operations.
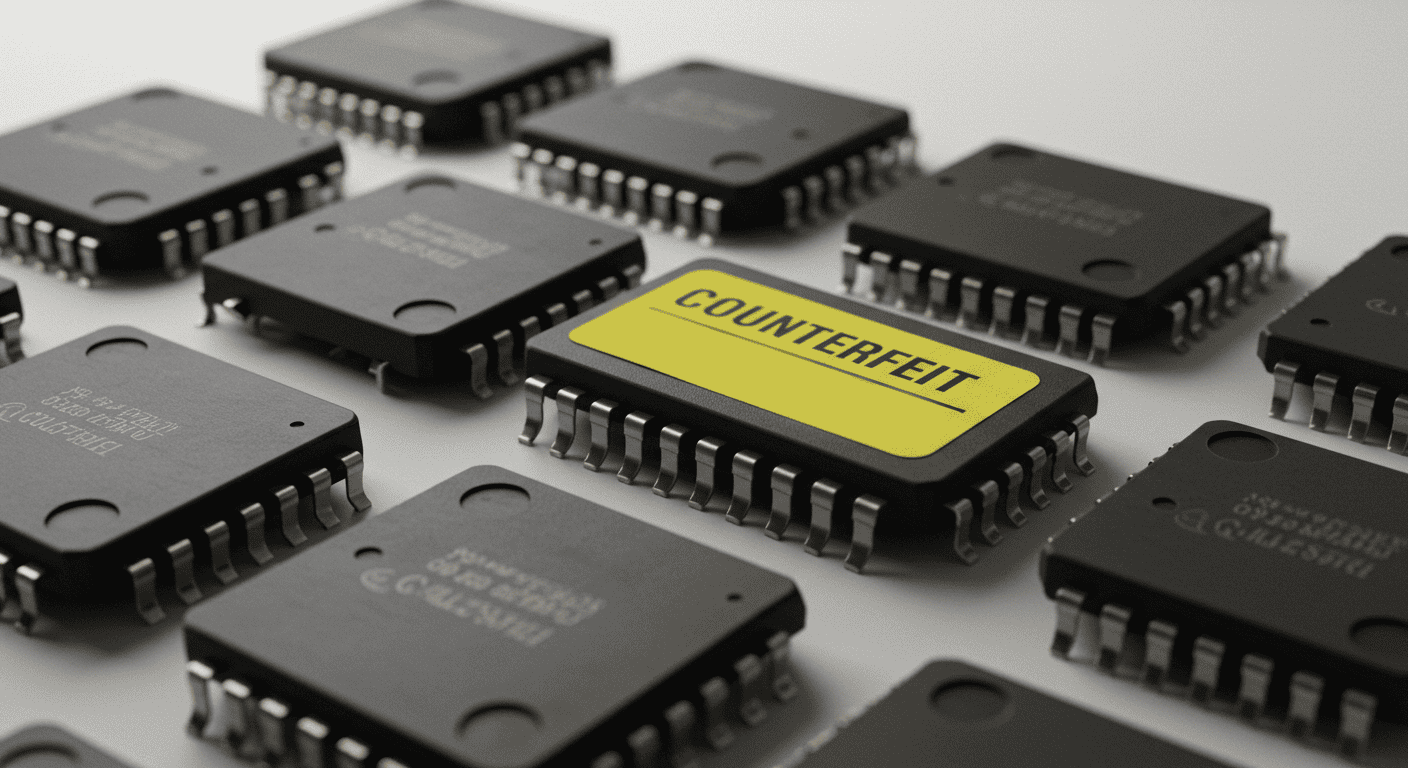
Measures to Mitigate the Risk of Counterfeits
Source from Authorised Suppliers: The simplest safeguard is to purchase components exclusively from Original Component Manufacturers or their authorised distributors. This minimises the risk of counterfeit products entering the supply chain.
Robust Testing and Inspection: Companies employ advanced testing methods to verify component authenticity. Electrical testing can also detect subtle performance anomalies.
Certification and Compliance: Industry standards such as AS6081 and AS6171 provide rigorous guidelines for counterfeit detection and prevention. Certification ensures that suppliers follow stringent quality control measures.
Partnerships and Intelligence Sharing: Collaboration between manufacturers, government agencies, and independent testing houses helps share intelligence on counterfeit threats.
The Role of Retronix in Safeguarding Supply Chains
At Retronix, we understand the importance of component authenticity and reliability. Our state-of-the-art electronic component testing services are designed to detect and prevent counterfeit infiltration. As a UKAS ISO 17025-accredited test house to AS6171 standards, we offer comprehensive testing solutions, including:
Visual Inspection – Detects discrepancies in markings, surface conditions, and general packaging.
X-ray Inspection – Reveals internal component structures, identifying tampering or counterfeits.
Decapsulation and Marking Verification – Confirms internal die authenticity by exposing and verifying the semiconductor die.
Electrical Testing – Evaluates component functionality to ensure compliance with manufacturer specifications.
Solderability Testing – Ensures components maintain proper connectivity in circuit board assembly.
Heated Chemical Testing – Identifies resurfacing, blacktopping, or other counterfeiting methods.
Material Analysis (XRF) – Verifies the elemental composition of component materials for authenticity.
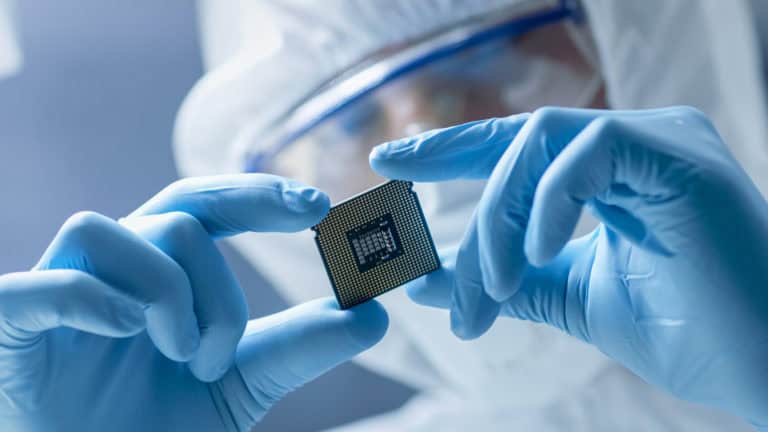
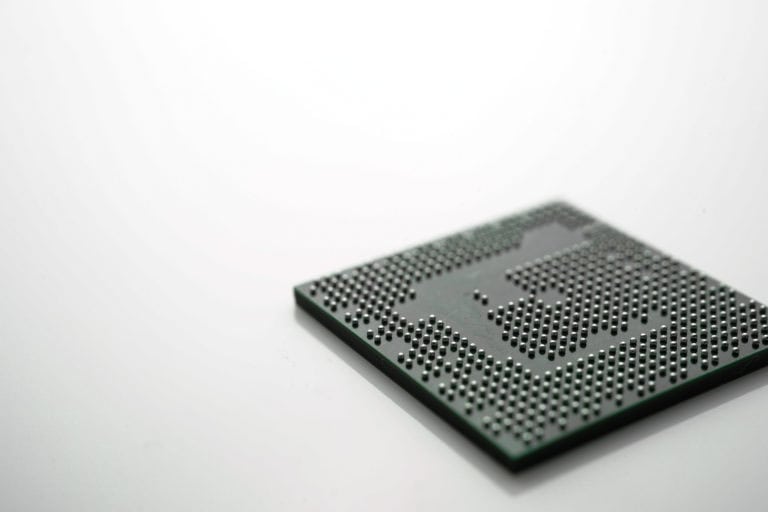
With decades of experience, we help companies maintain a secure and reliable supply chain and ensure components meet stringent industry standards.
Counterfeit electronic components pose significant challenges to industries worldwide. Companies can safeguard their supply chains by implementing best practices, embracing technological advancements, and collaborating with trusted partners like Retronix.
To fight counterfeits, we need to stay alert, be creative, and work together. Making sure parts are genuine isn’t just about profits; it’s about keeping things safe, reliable, and trustworthy.
If you need more information, feel free to reach out! You can use our contact form, email us at contact@retronix.com, or connect with us on social media. We’re here to help!