Case Study: Navigating Complex PCB Modification for High-End Automotive Supplier
Background
A renowned name in the automotive industry, faced a significant challenge with the need for complex Ball Grid Array (BGA) modification rework on Printed Circuit Boards (PCBs) essential for their operations.
The company’s engineering team successfully verified the modification on a small quantity in-house. However, the sheer volume required by their high-end automotive supply chain made it unsustainable for the internal team to handle alone.
The Challenge
The primary issue revolved around two critical problems identified in the PCB’s
- Ground Connection Issue: Under a component, one pin was improperly connected to the ground, necessitating disconnection.
- Memory Reporting Error: Bank 2 Memory on the PCB, specifically under the same component and near DDR Chip, was reporting a FLIP BIT error, requiring intricate modification under the DDR Chip.
The task demanded not only the removal and reballing of a 780-pin BGA but also precise track cutting, wire modifications, and the fitting of a new component—all while ensuring the utmost precision and reliability essential for automotive applications.
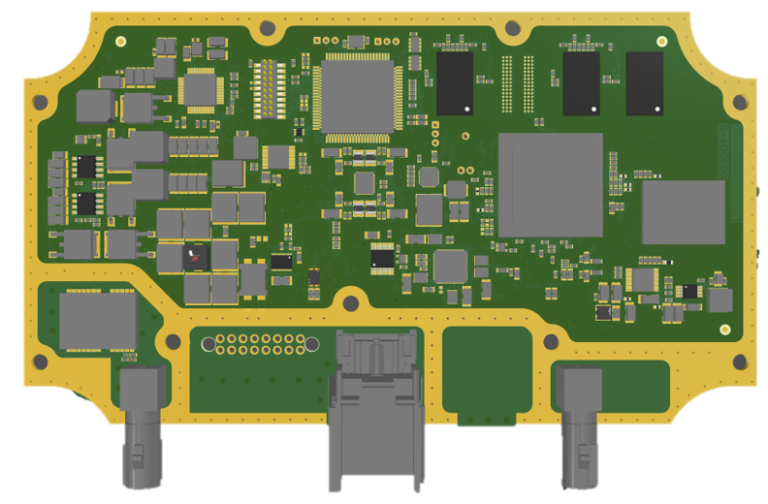
Remove the DDR3 device
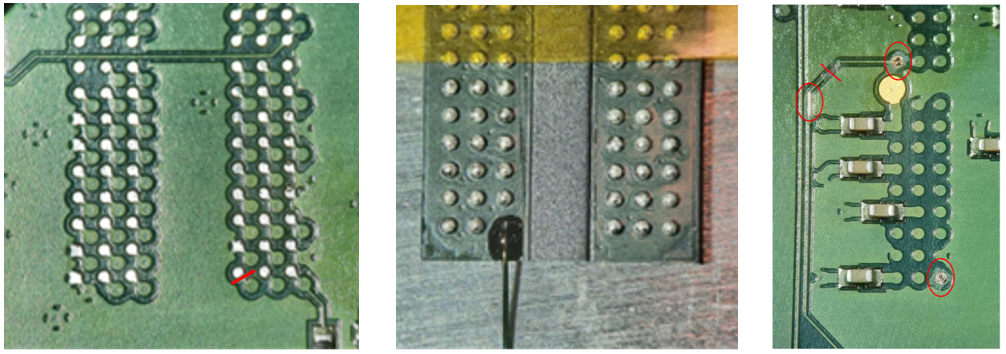
- Cut Track between BGA pad and the via
- Add wire to the BGA device pad – secure with epoxy
- Cut track to reverse side of the PCB – remove resist to the 3 locations shown.
Retronix Value
Recognizing the complexity and scale of the task, our customer turned to Retronix, a trusted partner known for our expertise in complex PCB reworks. A brief online meeting the customer to relay the urgent modification requirements to the Retronix team, who swiftly provided a comprehensive quote, maintaining open lines of communication throughout the process.
Understanding the critical nature of the modifications, Retronix dedicated its weekend to completing the first batch of modified PCBs, allowing the customer to test and approve the modifications promptly.
This swift response and successful initial batch set the stage for larger-scale production, effectively alleviating the pressure on the customer’s internal engineering team and enabling them to focus on ongoing development activities.
Retronix tackled the project with meticulous attention to detail, executing the following steps:
- Removal of the BGA 780-pin and subsequent reballing.
- Preparation of the PCB, including cutting a track between two pads and applying resist over the cut track.
- Reinstallation of the newly reballed component, followed by X-ray verification.
- Removal and disposal of a component, cutting of three specific tracks, and exposure of top-level tracks for new connections.
- Implementation of wire modifications under the component for external connections on the same side, including modifications through vias to the bottom side of the PCB.
- Installation of a new component and final X-ray inspection to ensure precise and accurate modification.
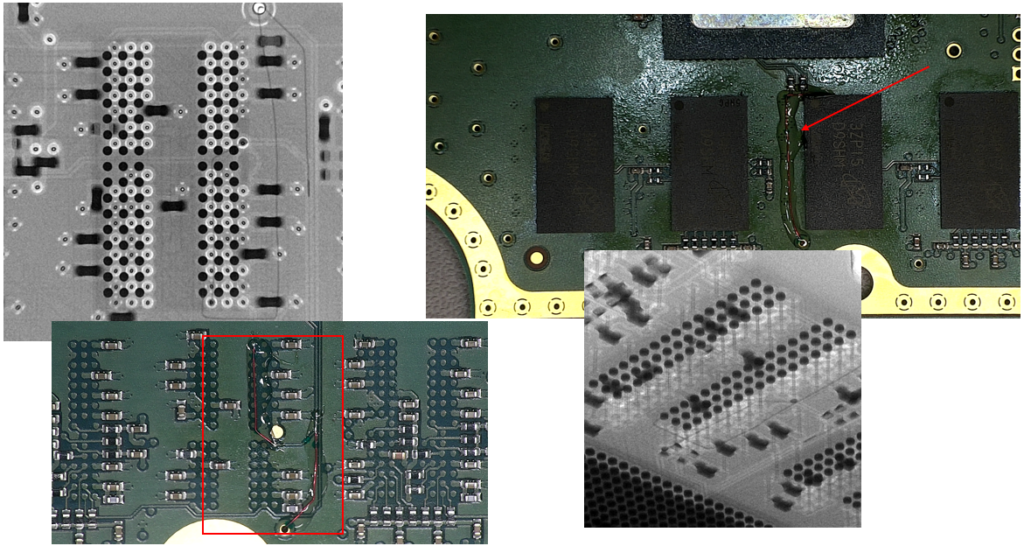
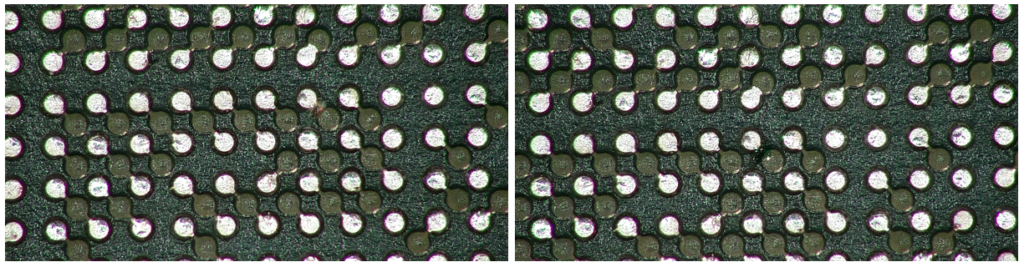
Conclusion
Through effective collaboration and leveraging Retronix’s specialized skills, the customer overcame a significant hurdle in their production process. The partnership not only resolved the immediate technical challenges but also ensured that the customer could maintain its commitment to innovation and excellence in the automotive industry. This case study exemplifies how strategic outsourcing for complex tasks can provide a pragmatic and efficient solution, allowing companies to focus on their core competencies while ensuring high-quality outcomes.