The Gray Market - Don't get Burnt by Counterfeit Chips
With the electronic component shortage predicted to last until at least 2022, Retronix has not only seen a significant growth of customer requirements for our testing services. But alarmingly, the quantity of counterfeit chips and suspicious components that we are detecting has risen significantly also. During any time of shortage, we observe a spike however, the severity of this particular supply crisis has dramatically worsened the counterfeit chip problem.
Playing with fire
The top manufacturers within the computing industry are lucky enough to receive orders directly from the chip manufacturers. However, manufacturers from other industries such as automotive, white goods, and medical electronics, source their chip stock from intermediary suppliers. Now because it is near enough impossible for these suppliers to obtain chips directly from the source, many have been exploring alternative channels. As a direct result, the gray market for semiconductors has grown, at an exponential rate.
“The gray market refers to the sale of products via distribution channels that are unintended, unofficial and unauthorised by the real vendor of the products.” Techopedia
Dubious sellers are taking advantage of the dire situation, luring in desperate buyers with the likes of search engine ads and swindling them fake chips under the guise of genuine stock.
The Danger of Counterfeit
According to Semiengineering, the counterfeit chip market is growing with a worldwide value of $75 billion. Hand in hand with the industry becoming more lucrative, counterfeiters are becoming more sophisticated in their techniques. However, the difference between genuine semiconductors and fakes semiconductors couldn’t be more extreme. As explained by the Semiconductor Industry Association, chip manufacturers spend billions of dollars each year developing, manufacturing, and testing products that will perform to the highest standards and reliability levels for many years.
Counterfeiters, on the other hand, will repurpose components from old electronic waste using crude and poorly controlled processes that churn out semiconductors with far higher failure rates. This inherently effects the long-term reliability of these devices and worryingly jeopardises lives since they are prone to fail at the worst possible moments, such as when car airbags need to deploy, defibrillators are used to apply shocks, or when aircraft are landing.
XIlINX Device our Test Department Detected as Compromised
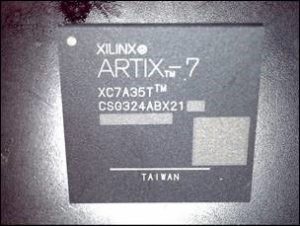
XILINX device with 2D barcode rubbed off
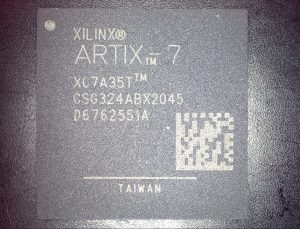
XILINX device with 2D barcode
Don't get duped by counterfeiters
Retronix has a test department dedicated to the identification of counterfeit parts along with the best tools for this process. We also have years of experience earned from dealing with this issue for numerous customer in varying industry sectors.
Due to the supply chain shortage, our test department has been uncovering new and inventive techniques that we have never seen. For example, we are starting to see chips with 2D Barcodes that have been laser-etched off. Suppliers will say that the 2D Barcode was only removed to conceal how the parts made it into the open market, encouraging desperate buyers to use the parts, assuring them the functionality of the devices will not be compromised. Don’t fall for it! Any device which has been visibly altered or changed should be considered compromised or counterfeit. This issue has also recently been raised by ERAI and more information can be found on a discussion on the ERAI: Counterfeit Part Avoidance, Detection, Disposition and Reporting Linkedin page.
If you have acquired components from an unverified source or are unsure about the authenticity of the parts, please get in touch with Retronix today.