Circular Economy - reclaim & reuse of electronic components
The global demand for electronics continues to grow.
The International Data Corporation forecasts that the internet of things, artificial intelligence, and virtual reality will drive worldwide spending on information technology to more than $1 trillion. In the digital age, electronic products are an indispensable part of our lives.
However, the fast pace of innovation and short product life cycles also mean that electronics often have a short user lifespan. This has led to a rise in e-waste as well as a loss of valuable resources locked inside these devices. Every year millions of tons of electronic devices end up in landfills instead of being recycled.
Reducing this waste and finding new ways to reuse or recycle old electronics could help reduce their environmental impact while also driving business value at the same time.
Industrial digitalisation and the circular economy are two important megatrends that can help drive innovation in the electronics value chain. The global market for electronic devices is estimated to be worth more than $177 billion in 2019.
As a result, companies operating in this sector now need to adopt new strategies to remain competitive in the digital age. One of those is adopting a circular economy approach, which involves principles such as sustainable production, reuse, and recycling of materials at every stage of their lifecycle.
By applying these principles to electronics, computers, server boards, hardware, internet of things, telecom electronics, and more, it’s possible to reduce not only waste but also recover valuable electronic components/devices that can be used over again in new products – creating a closed loop system where nothing is wasted and everything has a second life somewhere else in the supply chain.
Circular economy thinking is everywhere these days. Innovation leaders in every industry embrace circular principles to reduce waste, cut costs and boost productivity.
Component recovery, re-use & circular economy solutions
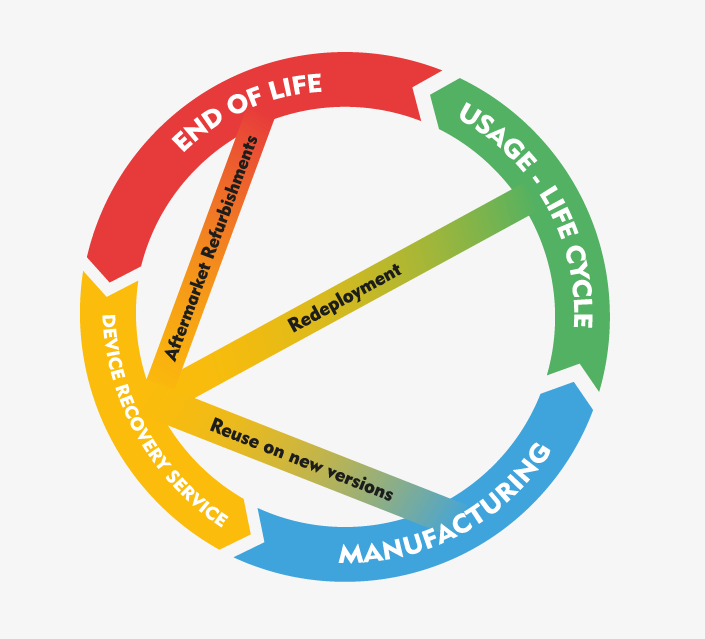
Manufacturing Stage: Re-integrate high-value components from fallout, end of life products, scrap – back into your supply chain.
Life Extension: Re-process, re-condition, refresh, test and verify components for aftermarket care and future sourcing.
End of Life & Re-sourcing: Recover your devices from scrap, prepare for re-use, test, validate and verify for integration in your refurbishment and manufacturing stages.
Circular Economy ethos of refurbish & re-use. This isn’t a new vision for Retronix – we have successfully been offering customers our recovery & re-use solutions for over 30 years.
Our wide range of services to the electronics industry allows us to offer a complete service for the safe recovery of parts ready for your new builds.
- 24 Hour Dry Bake
- Visual Inspection
- Safe Device Removal
- Coplanarity Checks
- IC Tests
- Visual Inspection
- Re-reeling & Re-packing
- 24 Hour Post Bake
Retronix has developed a process to recover and refurbish these electronic components including BGAs, to enable reuse. This process meets the component manufacturer’s specifications of maximum reflow cycles allowed on an electronic component, adhered to extensively by both OEMs and CEMs.
In 2021 Retronix recovered nearly 3 million components from approximately 650,000 PCBs that would otherwise have gone to scrap or landfill. We expect this number to double this year due to the ongoing supply chain disruptions, more organisations discovered Component Reclaim as a viable and valuable solution to their component sourcing issues.