Ensuring Military-Grade Durability : The Importance of Component Recovery, Laser Reballing & Automated Retinning in High Reliability Electronics
In high reliability sectors such as aerospace, defense, security, and space, failure is not an option.
These sectors demand components that can withstand extreme temperatures, vibrations, and radiation among other external stresses. Component preparation solutions like chip recovery & reuse, laser reballing, retinning can help extend the life of these critical components.
Chip recovery involves removing and testing for root cause of failure, the information can then be used to improve the design and quality of future components. It can also lead to cost savings by identifying components that can be repaired rather than replaced new, this safeguards the supply chain against counterfeits, and reduces long lead times on critical components.
Laser reballing and Automated retinning involves applying a new layer of solder (Pb or Pb Free) to legs of the device or spheres in case of a BGA, this can help in increasing the reliability of the component by reducing the risk of solder joint failures and mitigating tin whiskers.
Overall, the automated high reliability component services can help ensure the safety and reliability of personnel and equipment, while also reducing costs and improving performance.
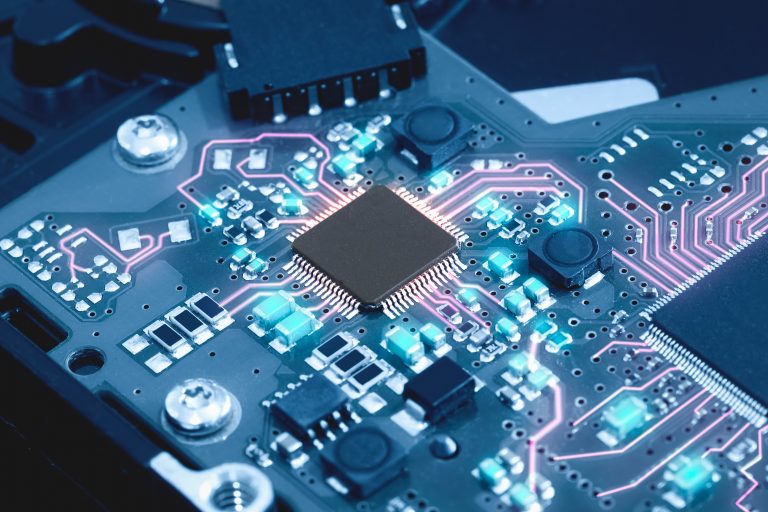
The Importance Of Military-Grade Durability In Electronics
The need for military-grade durability in electronics is paramount, especially in sectors such as aerospace, defense, security and space. Electronic components in these sectors must endure harsh environments, including extreme temperatures, vibration and shock.
They must also operate reliably and safely in critical applications; where failure can lead to catastrophic consequences. Therefore, it’s essential to ensure that electronic components are not only repaired but also restored to military-grade durability.
The requirements for military-grade durability vary depending on the sector and the applications. For example, aerospace and defense sectors may require chips to meet the MIL-STD-883 or MIL-PRF-38534 standards.
Component Recovery & REUSE
Component recovery is the process of removing electronic components from a circuit board or other electronic devices for reuse or recycling purposes. The process involves the use of specialized equipment and techniques to remove components safely and effectively without damaging them, i.e using minimal thermal stress.
The benefits of component recovery are many. It allows for the reuse of expensive chips and reducing cost of repairs. It also reduces the lead time for replacement components and safeguards supply chains against counterfeits. Additionally, it reduces e-waste which is beneficial to the environment.
Component reclaim is a critical process and it is essential that it is done exactly in conformance with the high reliability standards to avoid damage to the chip set.
Laser Reballing
Laser reballing is a process of restoring the solder balls on a component to their original condition or the desired solder alloy. This process is necessary when the solder balls on a component have been damaged, removed, or if the solder alloy needs changed. Laser Reballing involves the use of a laser to attach new solder balls to the component.
The benefits of laser reballing are that it allows for the reuse of expensive BGA’s reducing the cost of repairs. It also reduces the lead time for replacement components. Retronix carry out laser reballing to the IEC Standard.
It ensures that the chips are restored to their original condition without using a reflow/thermal cycle – therefore it meets the required standards for military-grade durability.
Automated Retinning (ROBOTIC HOT SOLDER DIP)
Retronix Automated Tinning Process is a state-of-the-art technology that offers an innovative approach to automated tinning, making the process faster, more efficient, and cost-effective.
Robotic hot solder dip technology is a process that involves dipping the component leads in a batch of the desired solder – the process is controlled by a robotic arm, which precisely dips the leads for a predetermined amount of time. The solder creates a strong and reliable bond between the leads and the circuit board.
This automated tinning process offers advantages such as consistency, precision, and improved quality control, making it an ideal solution for various industries, such as aerospace, defense, security & space.
Choosing the Right Service Provider
When choosing a service provider, it’s essential to consider their experience, expertise, and equipment.
Retronix Global, Inc. is the perfect service provider for component preparation services in electronics for the US Military market. Retronix has been in the electronics industry for over 30 years and has built a reputation for quality and reliability.
Retronix has invested in state-of-the-art equipment and technology that allows us to recover, reball, and repair electronic components with precision and accuracy. We have a team of highly trained professionals who can handle complex projects, ensuring that they meet the highest standards of quality.
The US Military market requires high-quality and reliable components, and Retronix understands this. We use only the best and most advanced equipment to ensure that all components are restored to their original specifications. We also have strict quality control measures in place including automated inspection systems to ensure that all components meet the required standards.
In conclusion, Retronix Global, Inc. is the right service provider for the US Military market. With our years of experience, state-of-the-art equipment and technology, highly trained professionals, and strict quality control measures, we are the perfect partner for any project. Our commitment to quality, reliability, and quick turnaround time makes us the go-to service provider for the US Military market.